Trimming Hydroformed Parts
Using shimmy die technology to finish trim parts
One of the many challenges in a hydroforming operation is trimming the parts. One method that often is overlooked is the use of shimmy dies. Available in one-, two-, three-, and four-motion styles, there are they are well-suited to trimming hydroformed tubes to length. They can eliminate chips, coolant, dust particles, and other potential hazards. In addition, demurring or wire brushing operations usually are not required with these trim dies.
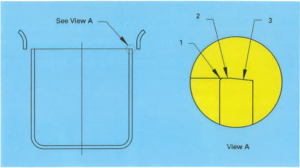
Shimmy dies perform a shear process that consists of three stages – plastic deformation, shear, and break. The arrows indicate the area in which these stages occur.
Although trimming dies are available in different types and styles, all of them use the same basic shear process (see Figure 1):
- Stage 1: Plastic deformation. Upon entry of the punch, the metal goes into a plastic like state, stretching and creating a slight radius.
- Stage 2: Shear. The shear is the flat part of the cut that normally is about 30 to 50 percent of the wall thickness of the material.
- Stage 3: Break. The break occurs when the shear strength of the material is exceeded and the scrap breaks away at the trim line. Any burr created typically is on the break side of the cut.
- One- and two-motion cam dies perform one of the two trim steps, respectively. Subsequent trim operations may require additional trim stations to complete the part. On the other hand, a four-motion shimmy die can perform the entire trimming operation at one station and with one stroke of the press. The trim line may be simple (flat) or complex (featuring contours, notches, or tabs).
A tube trimmed and the scrap ejected from this four-motion-style shimmy die. This type of die – regardless of the number of motions – is compatible with any type of mechanical or hydraulic press that provides cushion pressure. If an air or hydraulic cushion is not available on the press, the die can incorporate an air or nitrogen cushion system.
Operations of the Die
As the press ram descends (see Lead-in illustration), the pressure pads make contact with the die plate. This drives the die and parts downward. At the same time, a series of cams drive the die and part horizontally toward the punch – the cutting member – from four directions. This action causes the scrap material to be sheared from inside toward the outside of the part, leaving virtually no burr on the outside. After trimming, the part and scrap can be ejected by air pressure out of the die.
This method of trimming results in a sheared edge with 100 percent material thickness at the trim line. Overall height tolerances from the inside of the part usually can be held to within a few thousandths of an inch.
Hydroformed or bent tubes can be odd shapes and sometimes longer lengths, it can be necessary to trim them horizontally (see cover insets). To accomplish this, a horizontal cam trimming machine can be used. By the use of cams, cushion pressure, and the horizontal stroke of the machine, a shimmy die shears through the part in four motions. A hydroformed tube to be trimmed is presented into the trim area and clamped in place. The punch travels forward then is driven outward in four directions. This movement is called the punch throw. As the punch moves across the face of the die, the scrap is sheared away, leaving 100 percent metal thickness at the trim line. When the punch retracts, the scrap drops downward, out of the trim area.
Die Parameters
Because the cam arrangement is characterized by four sides and moves in four directions, there is a limit as to where notches and tabs can be positioned at the trim line. For example, a round part having four notches or tails on the centerline is a good candidate for this process. However, a round part having 12 notches equally spaced is not a good candidate.
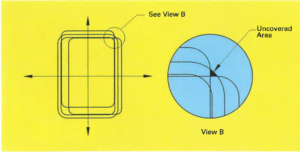
For rectangular parts, the corner radius should be at least five times the material thickness. This allows total coverage in the corners as the punch travels across the die face.
Square or rectangular parts also can be trimmed. On rectangular parts, the corner radius should be at least five times the material thickness. Following this guideline is not absolutely necessary, but it helps to reduce reliance on the break portion of the cut to complete the trim (see Figure 2).
Notches, table, and different trim levels can be trimmed, too, if there is no change in elevation near a corner. The amount of shear and break (see Figure 2) can be varied by adjusting the die clearance, which is the distance between the face of the punch and die cutting surfaces.
Part Parameters
When trimming hydroformed tubes, consideration must be given to the design of the hydroform die because it will determine how the tube will be processed after hydroforming. Net-shape hydroforming of the seal ends of the tube is the most desirable condition. This is advantageous for cam operation, and it reduces wasted material and the cost of pretrim operation.
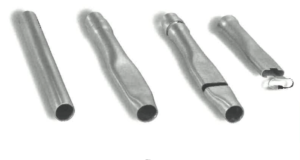
A Shimmy™ die can perform two operations-in this case notching hydroformed tube (rightmost illustration)-as the final step in a tube fabricating process.
If the shape, or geometry, of the seal end differs from the trim line geometry, the seal end must be cut away (see Figure 3). This allows the tube to enter the die cavity and the punch to enter the tube. Shapes or notches that cannot be saweed can be incorporated in the trim line of the cam operation in this matter.
Applications
The operating concept of a shimmy die is relatively simple. However, because the process is used for an array of part sizes, trim line shapes, and stock thickness, each part must be evaluated individually. Shimmy dies can trim any type of material that can be pierced or blanked, ranging from 0.005-inch brass to 0.250-inch steel. The process can be used to trim parts that are delicate, such as titanium heart pacemakers, or very robust, such as automotive tubular frame rails. Families of parts can be run in the same basic die with a simple tool change.
Applications for shimmy die technology
Patented in 1940 by Charles M Brehm as the Shimmy die, the four-motion cam trim die has been used in a variety of industries, including automotive, appliances, chemical, agricultural machinery, and construction machinery.
Although the concept is 60 years old, it has found new application in hydroformed tubes. Because the hydroforming process work-hardens the tube, cam trim dies – which can be made of tool steel hardened to Rockwell 60 (C) – are a good match for this technology.
We Design and Build Single Dies Entire Manufacturing
Products
- Automatic Manufacturing System
- Special Machines
- Brehm® “Shimmy” Die
- Brehm® Tube Cutting Machines
- Ringmaster™ Tube Cutting Machines
- Vulcanaire® Grinding Attachements